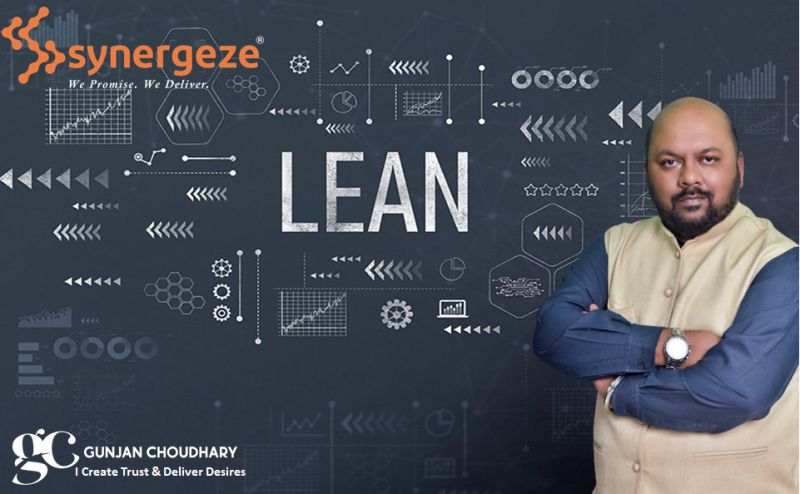
Small businesses at times seems to be ignoring many a thing, by just treating them as one more jargon in this new age of super complicated words and synonyms.
Process Re-Engineering can be a game changer to businesses, as it can perform miracles on a failing or stagnant company and open new doors for a company on steady path of growth. However, the process is tricky and needs some pain-killers to supress the pain of change and pain of tearing down what we are used to and feel comfortable with.
If ignoring this was a mistake, the next big mistake could be to settle for a cheap and basic process re-engineering tool in absence of an expert guidance. It could be that you tried saving a cent and lost a dollar.
We atΒ Synergeze Consultants Private Limited, help businesses to implement the changes in an ongoing manner without effecting the current operations in any way and yet delivering the desired results. To learn more about our standardised approach which is customized for every single business please reach out to us.
If you wish to be more profitable and save on all forms of costs β
Your destination is our name βΒ Synergeze Consultants Private Limited.
Share
Having discussed the first 2 steps in yesterday’s post let’s look at the remaining steps today…
3. πͺπππππ πͺπππππππππ πΎπππππππ
After mastering our value stream, we need to make sure that each team’s workflow remains smooth. Keep in mind that it may take a while.
Developing a product/service will often include cross-functional teamwork. Bottlenecks and interruptions may appear at any time. However, by breaking up work into smaller batches and visualizing the workflow, we can easily detect and remove process roadblocks.
4. πͺπππππ π π·πππ πΊπππππ
Having a stable workflow guarantees that your teams can deliver work tasks much faster with less effort. However, in order to secure a stable workflow, make sure to create a pull system when it comes to the Lean methodology.
In such a system, the work is pulled only if there is a demand for it. This lets you optimize resourcesβ capacity and deliver products / services only if there is an actual need.
Letβs take a restaurant, for example. You go there and order a pizza. The baker pulls your order and starts making your pizza. He doesnβt prepare tons of dishes in advance because there isnβt actual demand, and these tons of dishes can turn into a waste of resources.
5. πͺπππππππππ π°ππππππππππ
After going through all previous steps, we already built our Lean management system. However, let’s not forget to pay attention to this last step, probably the most important one.
Remember, our system is not isolated and static. Problems may occur at any of the previous steps. This is why we need to make sure that employees on every level are involved in continuously improving the process.
There are different techniques to encourage continuous improvement. And the best one being, every team having a daily stand up meeting to discuss what has been done, what needs to be done, and possible obstacles.
We shall continue this discussion…. However if you wish to know more and you are in real need of a Process Expert dealing in Lean Management please reach out toΒ Synergeze Consultants Private LimitedΒ or DM me and we shall be glad to hold your hand and walk together.